What are the infrared optical materials?
Infrared optical materials are typically classified into three main categories: infrared optical glass, infrared optical plastics, and infrared optical crystals.
1. Infrared Optical Glass
The advantages of infrared optical glass is good optical uniformity, can be melted and processed into any shape under high temperature conditions to meet the requirements of the designer to use. At the same time, this material has high mechanical strength and hardness, easy to process, high chemical stability, corrosion resistance, wear resistance, and raw materials are easy to obtain, low cost. However, it has a narrow transmission band and is susceptible to melting and damage under high temperatures. Examples include oxide glasses and chalcogenide glasses.
Infrared optical glass is generally classified into two main categories: oxide glass and chalcogenide glass. The most commonly used oxide glasses include sapphire (Al2O3)
and quartz (SiO2). Due to the existence of strong absorption bands at 3μm and 7μm, the long wavelength limit of oxide glass transmittance is not long, so it can only be used in the visible, near-infrared, short-wave infrared and mid-wave infrared wavelengths. The most commonly used chalcogenide glasses include germanium-arsenic-selenium glass (Ge33As12Se44) and germanium-antimony-selenium glass (Ge28Sb12Se60). Chalcogenide glasses replaces oxygen with group VI elements S, Se, and Te to enhance long-wavelength limit, which are suitable for short-wave, mid-wave, and long-wave infrared bands.
2. Infrared Optical Plastics
Common infrared optical plastics include polyethylene, polypropylene, polytetrafluoroethylene, and others, which are amorphous high-polymer. The low transmittance of plastics in the mid-wave infrared is due to the fact that the rotational and lattice vibrational absorption bands of their molecules lie exactly in the mid-wave band. Plastics have higher transparency in the near-infrared and long-wave infrared bands. Infrared optical plastics have many advantages, such as low cost, corrosion resistance, and are not easily soluble in water. Fresnel lenses in infrared alarms are often made from long-wave infrared plastic materials.
3. Infrared Optical Crystals
For infrared optical systems, there are two common types of infrared crystal materials: ionic crystals and semiconductor crystals. Compared with infrared optical glass, infrared crystal materials are characterized by longer wavelength transmission limits, larger differences in Abbe number and refractive index coefficients, and distinct physical and chemical properties. Common ionic crystals include oxide crystals, alkali halide compounds, and infrared halides. Common semiconductor crystals include germanium, silicon, zinc sulfide, zinc selenide, etc.. Due to the typically higher reflectance of semiconductor crystals, anti-reflection coatings are generally required. The following provides an overview of some commonly used semiconductor crystals.
Germanium has a wavelength range of 1.8 to 23 μm, and the diameter of germanium single crystals is usually around 250 mm. It has good chemical stability. The hardness of germanium is low, so special attention is needed during producing and processing. Owing to the high temperature coefficient of its refractive index, it cannot be used beyond 150°C. Additionally, due to the high refractive index, the loss of reflected energy is large, anti-reflective coatings are needed. Germanium can be used to make lenses, windows and filters.
Silicon is a non-metallic crystalline material with a single crystal diameter exceeding 150 mm and a polycrystalline diameter up to more than 400 mm. Silicon has significant advantages over germanium in terms of strength, hardness, and resistance to thermal shock. The upper limit of silicon's operating temperature is 325°C. Its refractive index is generally around 3.4, requiring the anti-reflective coatings. In addition to its use in lenses and windows, silicon can also be employed for fairing.
Zinc selenide has a wavelength range of 0.5 to 24 μm and is a common infrared optical material with stable chemical properties, but relatively soft physical, usually requiring the deposition of high-strength anti-reflective coatings, which can be utilized for lenses and windows.
Zinc sulfide has a wavelength range of 0.4 to 18 μm and exhibits a light yellow color under sunlight. It is usually processed by vapor deposition for use in lenses, windows, and fairing. Table 1.0 provides the refractive index of infrared optical crystal in different bands.
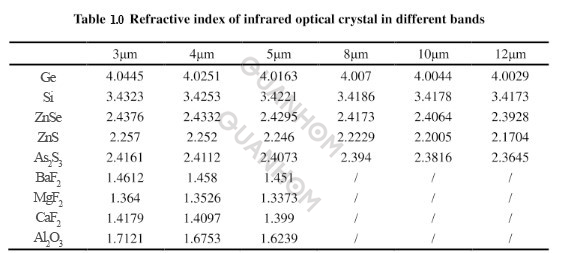
For infrared optical systems, the selection of infrared materials is as important as the initial structure. When selecting materials, designers should first refer to relevant information, analyze the characteristics of each material in optical, mechanical, chemical and other aspects, and make reasonable choices based on the actual operating environment of the infrared optical system while meeting design requirements. In general, there are fewer infrared optical materials that simultaneously take the above points into consideration.
When selecting materials, it is essential to note that the higher performance parameters of the material are not always better, and lower parameters are not necessarily preferable. For instance, reflective mirrors require materials with high reflectivity, while lenses need materials with low reflectivity and high transmittance; windows for cooled infrared detectors require materials with low refractive index. The materials for the beam splitter need a low Abbe number to achieve high dispersion, and the doublet lens requires a combination of low and high Abbe number materials.