How to Design and Select the Infrared Thermal Imaging Camera Used in the Measurement Field?
In most cases, objects have higher contrast in infrared spectroscopy, which helps users to better distinguish them from the background. For example, if a user tries to track an airplane or missile, the infrared radiation of their hot engine in the cold air becomes more prominent. The strong contrast makes it easier for the tracking algorithm to lock the target and maintain effective tracking during the entire flight.
Infrared thermal imaging cameras (infrared spectrometers) can be used to determine the characteristics of a target in a certain brand of the infrared spectrum. Infrared thermal imaging cameras can measure the accuracy of hitting the target. Some infrared thermal imaging cameras can not only image the target but also the target can be laser marked. The following factors need to be considered when designing and selecting thermal imaging cameras suitable for a specific job.
Responding speed
Most infrared optical cameras used for shooting range measurement observe high-speed moving targets. For example, if the integration time of an infrared thermal imaging camera (similar to the exposure time in a visible light camera) is too long, you may miss the measurement of a high-speed moving target, or the target is smeared in the image to produce a smear, and you may not be able to get an accurate measurement.
Similarly, when using a thermal imaging camera to observe an object that appears instantaneously, such as a spark suddenly appearing, its speed is faster than your integration time, and we will not be able to fully describe events such as these. In short, when capturing high-speed targets or events, a faster frame rate will provide a more accurate measurement.
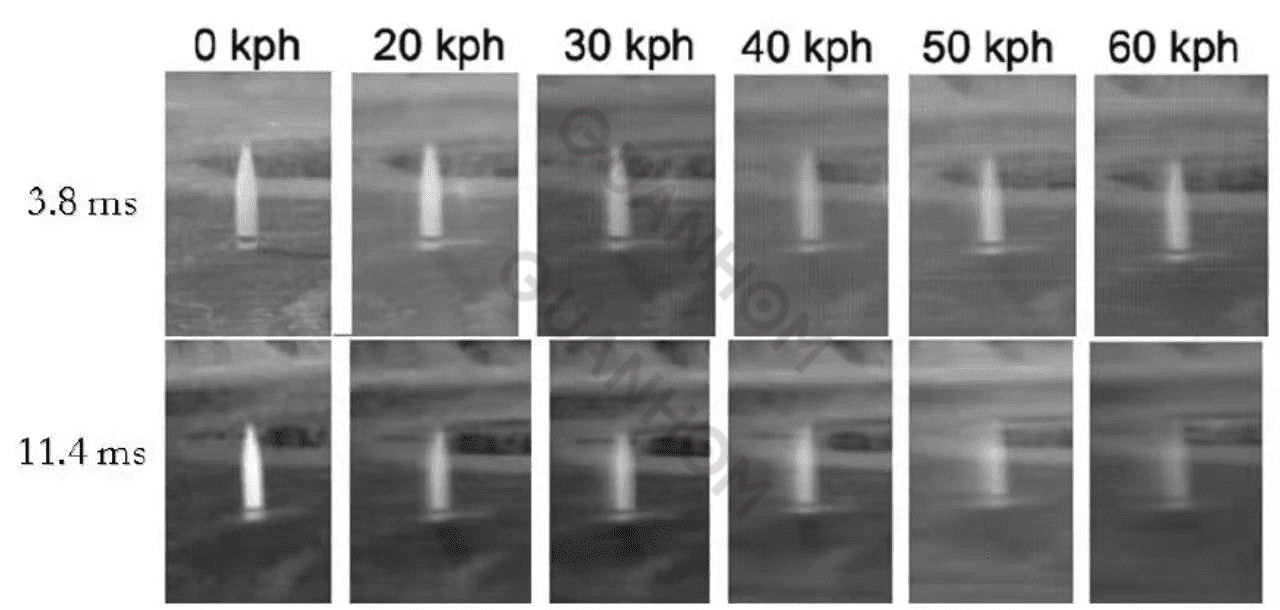
(1) Frame rate technology
Based on the new detector technology, the frame rate of thermal imaging cameras has been greatly improved in the past two to three years.
The sensitivity of the infrared thermal imaging camera has also been greatly improved. Accordingly, its integration time can be shortened. This also means that users can use them for applications that may not have been considered before, such as ballistics research or ammunition research. These new thermal imaging cameras can capture bullets in flight or track, and describe explosion events.
Even if the observed target is not so fast, a higher frame rate is still very beneficial. Suppose you need to shoot some targets at 100 frames. When capturing this target at 400 frames, you can apply a quadruple frequency-time domain filter to reduce noise and get data of 100 frames.
(2) Spectral response of the imaging
Different types of thermal imaging cameras have different working bands. To a large extent, infrared cameras can be divided into two types of applications, one for short-wave infrared (SWIR) imaging for radiometric measurement, and the other for mid-wave (MWIR) infrared and long-wave infrared (LWIR) for thermal measurement.
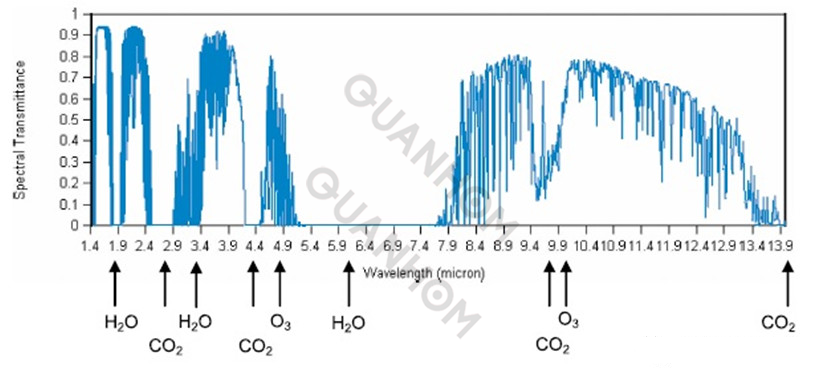
In the range of 0.9 to 1.7μm, short-wave infrared imaging can observe directional energy (laser) radiation, target imaging, and characteristics. Laser-directed energy weapons are a good example. In this case, short-wave infrared band imaging is usually used to measure radiant energy or qualitatively determine the performance of these devices.
For thermal measurement, thermal imaging cameras tend to work in two wavelength ranges, MWIR with a wavelength of 3 to 5 μm or LWIR with a wavelength of 7 μm to 14 μm. These two spectral ranges have their own characteristics. For example, the advantage of mid-wave infrared lies in its superior thermal contrast and sensitivity. Compared with long-wave infrared, the temperature change is small, but the radiant energy changes greatly.
The core advantage of long-wave infrared is that it covers a wide temperature range within a certain integration time. For example, the standard calibration range of a mid-wave infrared camera that does not use a spectral filter is -20°C to 350°C. In contrast, the standard range of long-wave infrared thermal imaging cameras can be extended from -20°C to 650°C.
Therefore, if there is a significant temperature change in a short period of time during the test, a long-wave infrared thermal imaging camera is a more appropriate choice. For example, a missile is very hot when launched, but when the propellant burns, its temperature will drop. The LWIR lens designed and produced by Quanhom uses good heat dissipation technology to ensure stable performance during work.
Spectral filter
There are two general types of spectral filters for thermal imaging cameras. One is a neutral density filter (ordinary filter), which attenuates the energy of the entire wavelength range to the same degree. It can calibrate the infrared camera to a higher temperature and radiation range, such as 3000°C.
Another type of optical filter is spectral filters, which will shield the radiant energy in a specific band, which is helpful for you to test in the band of interest. For example, shooting and tracking a chemical gas plume visible only in a narrow area of the spectrum, or wanting to depict a target through the target flame. Under normal circumstances, the heat generated by the flame will occupy the main part of the image, but the spectral filter can shield it, allowing you to see what you want to see.
Cold filters and warm filters
The infrared camera can put the infrared filter in a certain position of the lens, or put the optical filter in the Dewar of the detector.
The advantage of installing the optical filter in the Dewar is that the reflection and radiation of the filter itself are very small, which is conducive to the control of thermal noise. The disadvantage is that once it is built into the Dewar, it cannot be easily removed or replaced.
The core advantage of heating filters in the lens is that they can be easily removed or replaced to reconfigure the thermal imaging camera for another test. However, the spectral filter at ambient temperature tends to produce artifacts in the image, which requires frequent updates to maintain image quality.
Spatial resolution
The spatial resolution of an infrared thermal imaging camera is one of the key factors for accurate measurement and obtaining high-quality images. Generally speaking, after imaging with a thermal imaging camera, the object of interest should occupy about 10 pixels in the smallest dimension. The two major contributors to this goal are the pixel size of the detector and the optical system.
(1) The pixel size of the detector
It is gratifying that the array size of infrared detectors has increased substantially in the past few years, and the pixel size of the detectors has continued to decrease. And now there are many commercial off-the-shelf thermal imaging cameras that can support very high resolution. The thermal imaging camera manufactured by Quanhom can support resolutions up to 1280x1024 (SXGA). In addition, the pixel size has been reduced by more than 50%, which means that under the same optical system and distance, the target can be imaged on more pixels, thereby improving image quality and measurement accuracy. Or you can choose a different optical system to obtain four times the original field of view without losing resolution.
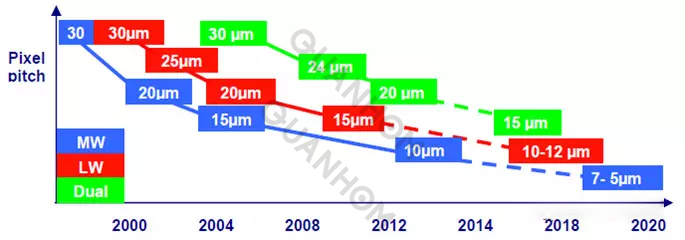
(2) Optical system
The second contributor to the increase in spatial resolution is the optical system. For long-distance testing, a long focal length lens is very important. In order to meet the test requirements for different distances, the optical system used in the thermal imaging camera should preferably have a continuous zoom function. The infrared continuous zoom lens designed by Qaunhom can arbitrarily zoom in and out of the target while keeping the target in the center of the field of view. This function is very suitable for tracking moving targets. It can maximize the pixels on the target while changing the focal length, and keep the target always in the center of the field of view.
In addition to the continuous zoom function, the infrared optical system used for measurement should be able to accurately and repeatedly read the focal length of the lens and its focal position during continuous zooming and mark the reading on the image, which makes the target's Spatio-temporal position Information application becomes possible. When tracking a target, the focal length of the camera is used to determine the target's position relative to you at any given time, and the focal length is associated with a single frame of an image, and the position of the moving target can be determined in the subsequent acquisition and analysis.
Atmosphere
Target radiation can only reach through the air and be imaged on the infrared thermal imaging camera. In addition to attenuating the target's radiation, air will also add some interference signals during the transmission process. In the infrared band, the atmosphere is transparent at some wavelengths, and opaque or semi-transparent at other wavelengths. Therefore, the infrared radiation measured by a target at a close distance is different from the radiation emitted from the same target at a long distance.
Most thermal imaging cameras are calibrated in factory laboratories based on objects a few meters away. In the range infrared camera you may need to observe less than one kilometer or one hundred kilometers or even thousands of kilometers away from the target, so the atmosphere this factor becomes important. In this case, relying on factory calibration is not enough. In order to provide accurate measurement, the infrared thermal imaging camera needs to be equipped with corresponding software to perform unevenness correction and radiation or temperature calibration.
Atmospheric compensation
There are two methods for atmospheric compensation. One method is to rely on the MODTRAN (Medium Resolution Atmospheric Transmission) model. This model is software developed by the Air Force for atmospheric modeling. MODTRAN can estimate the attenuation in the atmosphere or the atmosphere itself. The amount of radiation produced. The other method is to use known radiation sources, such as long-distance large-area black bodies, to perform atmospheric compensation through experiments.
Software
Most thermal imaging cameras used for shooting range measurement are remotely controlled, almost without direct control. Therefore, the control software is the only way for you to interact with the infrared camera, through the software to control, view, record, analyze and share data. Software is as important to the success of testing and measurement as the thermal imaging camera itself.
The control software used by the thermal imaging camera must be able to capture the original radiation or temperature data, so a key feature in the software is the ability to quickly and easily change between these measurement units.
As mentioned earlier, the continuous zoom optical system needs to read out the precise focus position and mark this data information on each frame of infrared image, these tasks also need to be completed by operating software. The control software allows users to analyze the data in a time-saving and labor-saving manner so that users can better analyze the test results and draw more meaningful conclusions from the test.
Another feature of the software is the ability to share data quickly and easily. At present, many applications will automatically generate task briefings after the test is completed, and users can extract and share the data of interest. The software must have a rich data interface, which can be interconnected with other software.
Taking into account all the above factors, we can choose the most suitable thermal imaging camera to provide accurate and high-quality measurement data for the target. If you want to know more about infrared optical systems after reading the above, you can get professional solutions by contacting us.
With excellent R&D technology and high-quality product services, we have quickly become one of the leading manufacturers of Opto-electromechanical components. We are committed to producing various thermal infrared lenses (including LWIR, MWIR, and SWIR). Our complete management system and strict quality inspection department can provide customers with safe and high-quality products. At the same time, our thoughtful one-stop service has also won unanimous praise from many customers. If you are interested in our infrared thermal imaging lenses, please contact us immediately!