The Performance and Design of Optical Thin Film
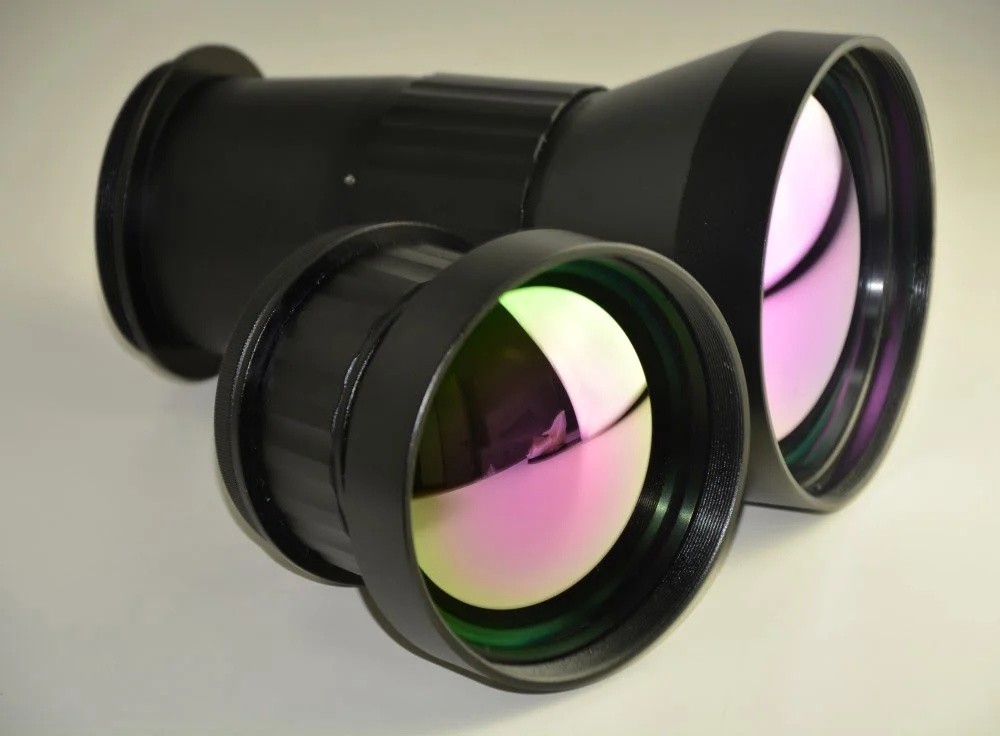
Almost all optical parts need to use optical thin films to change their transmission or reflection characteristics in optical systems. Although optical thin films are ubiquitous, many designers of an optical system are not familiar with the trade-offs in thin-film design or use or do not understand the characteristics of various thin film deposition technologies. The following is a detailed introduction of the important optical thin film design and related optical thin film deposition factors.
The optical thin film comprises layers of materials with a high refractive index and low refractive index. Its working principle is to use light interference to enhance the transmission of one or more wavelengths or preferentially reflect, or transmit a polarization to complete these tasks. Layers sometimes contain dozens of layers or hundreds of layers and are composed of many materials with different refractive indices.
However, the materials available to the film designer are not unlimited, which means that the actual coating must be constructed with a limited refractive index. In addition, the deposition process of the coating cannot completely accurately control the thickness and refractive index of each layer.
Therefore, optical design engineers must understand the performance of various optical thin films, such as the film’s cost-effectiveness, the effect of transmittance on the system, environmental adaptability, and the ability to resist laser damage. The following is an introduction to the performance and design of various optical thin films and optical thin film deposition schemes.
Anti-reflective coating (AR)
The performance of an anti-reflective coating (AR) is usually specified by the average transmittance of a single wavelength or a range of wavelengths, and of course, it can also be measured by the maximum remaining reflection allowed by the designer. For specific optical materials, the absorption coefficient of the material is fixed.
It may be more reasonable for some special occasions to use the maximum allowable residual reflection to measure. For single wavelength, single incident angle AR film, it can obtain very high performance. For example, on the surface of optical glass, in the visible light band, it is widespread that the residual reflection of each surface is less than 0.1%.
As the number of layers increases, the residual reflection on the surface decreases (the transmittance increases), but the spectral width range also decreases. As the spectral bandwidth or incident angle increases, the high performance of AR films becomes more and more challenging to maintain.
Therefore, as an optical designer, it is necessary to know whether the specified performance is the peak transmittance (remaining reflectance) or the average transmittance (remaining reflectance) in the entire spectral range or incident angle range. Otherwise, a little mistake may cause a huge impact.
For non-zero angles, especially for AR films above 30°, the polarization state of the incident light has a significant impact on the design and performance of the coating, and it is essential to determine the polarization state of the incident light. In the case of all non-zero incident angles, S-polarization has higher reflectivity on the surface of the medium than P-polarization.
Therefore, if there are inclined components in the system and require a relatively high transmittance, the optical designer should use the corresponding optical. The structure allows the optical component to encounter P-polarized light.
As the angle of incidence increases, the performance of the AR film shifts to shorter wavelengths. For example, an AR coating designed to produce the minimum reflectivity at normal incidence provides the smallest at a shorter wavelength at an incident angle of 45°.的Reflectivity. On a lens with a small radius, the incident angle at the center is 0°, while the incident angle at the edge may be 70°.
Even if the optical system uses a single wavelength, the AR film must have high performance in a wide spectral range. Even with With the increase of the angle of incidence, when the film response shifts, it can still perform well at the nominal wavelength. In fact, for optical surfaces with a small radius, special means or tools may be required to maintain consistent performance. Therefore, some trade-offs are needed between the complexity, cost, and performance of the film.
Because of the limited number of materials that can transmit visible light and infrared simultaneously, it is incredibly challenging to design and plate an AR film that works in the visible and infrared bands at the same time.
Multi-band AR films are very common in military optical systems. Achieving high transmittance across a wide band is relatively easy to achieve high transmittance for several specific wavelengths, and the cost will also be reduced. In addition, the design can analyze the specific requirements of the system for each band, specify the relatively high performance of one wavelength, and relax the requirements of other bands, which can also achieve a multiplier effect.
High reflective film
High reflective film can be realized in three ways: metal film, metal/dielectric film, and dielectric film. The advantage of a metal film is that it has good performance in a wide spectral range. For example, the reflectivity of aluminum reflective film in the range of 400nm to 10μm is greater than 85%, and the reflectivity of gold reflective film from 2μm to far-infrared is more excellent than 99%. It is almost impossible for all dielectric membranes to reach this level. In addition, the difference in reflectivity between the S polarization and the P polarization of the reflective metal film is usually much smaller than that of the dielectric film.
However, the peak reflectivity of the reflective metal film is less than the peak reflectivity of the dielectric film. Even the gold reflective film with 99.5% reflectivity in the infrared band cannot be compared with the dielectric film. The dielectric film can provide 99.99% at a single wavelength. Even higher reflectivity. The small amount of absorption of the metal film limits its peak reflectivity, which causes an important use limitation of the metal film, and the laser damage ability is not as good as that of the dielectric film.
The metal film's physical durability (abrasion resistance, damp heat, salt exposure) is not as good as that of the dielectric film. For example, in silver reflectivity, in order to prevent oxidation, its surface must be covered with another material, reducing its reflectivity.
For all highly reflective components with dielectric films, when specifying extremely high (>99.995%) reflectivity, the surface quality of the component must be considered because surface scattering becomes the main factor limiting performance, and the roughness of the optical surface must be specified, super smooth surface Special polishing and testing techniques are also needed, and the corresponding cost will rise.
Spectroscopic film
The performance of the spectroscopic film depends to a large extent on the structure of the spectroscopic element. There are generally two types of structures of the spectroscopic element, cube-type or flat type. The cubic structure is preferred for unpolarized light, which is inherently less sensitive to input polarization than the flat panel type.
On the contrary, the polarization beam splitter can use the inherent difference between S polarization and P polarization in reflection to achieve very high performance. Flat polarizers are always configured to reflect S polarization through P polarization and usually work best when the Brewster angle (the P polarization reflection coefficient drops to 0). For visible light wavelengths and optical glass substrates, this angle is greater than 56°.
It is much easier for flat-plate or cube-shaped polarization beam splitters to eliminate S-polarized light in the transmitted beam than to keep P-polarized light away from the reflected beam. That is to say, for visible light, the transmission extinction ratio of 10000:1 is OK. It is difficult to achieve a reflection extinction ratio greater than 100:1. These performance characteristics should be kept in mind during the system design process.
In the beam splitter, several factors can cause the complexity of the coating. For example, as the incident angle increases, the difference in reflectivity between S polarization and P polarization becomes larger, making it difficult to provide mirrors with the same performance for both polarization states. Therefore, it is advantageous to deal with only a single polarization in this case.
If unpolarized light is unavoidable, it is best to design an optical system where the beam splitter works at a smaller incident angle to minimize the effect of beam splitting. The spectral range (spectral bandwidth) is also an important factor. For the leftmost polarization-insensitive film, the spectral range of which exceeds ±10% of the center wavelength (for example, 550nm ±50nm) is a huge challenge.
Also important is how the tolerances of the beam splitter are specified. For example, there is a big difference between a beam splitter that must maintain its nominal performance within a 45°±5° incident range and a beam splitter that must achieve the nominal performance within the same range.
In the first case, the performance of the beam splitter must meet the incident angle range of all angles exceeding 40° to 50°; in the second case, the performance of the beam splitter is only satisfied within the range of 40° to 50°, and the user will The beam splitter components were put into their system and tilted adjustments to achieve the required performance. The requirements of the beam splitter in the first case are much more demanding than those in the second case.
The cube beam splitter is made of prisms by bonding and gluing, introducing wavefront errors, thereby affecting performance. In addition, absorption in the adhesive will cause scattering, which significantly reduces the laser damage threshold. (At present, some manufacturers use activated covalent bond technology (ACB) to avoid the influence of adhesives)
Demand for military films
The specific functions required by military requirements often pose severe challenges to the film. For example, some optoelectronic systems usually work in multi-spectral bands, which cover visible light (400nm~600nm), eye safety laser (1.54μm), and mid-wave infrared (3μm~5μm), etc. These layers of optical films are also often specified to function in a large range of incident angles and are polarization insensitive.
In order to minimize the size and weight of the system, especially in portable and airborne systems, optical engineers may compress the diameter of optical components, increasing the power density of the laser beam. Therefore, the laser damage threshold is also one of the issues that need attention.
In order to achieve advanced functions, optical thin films may need to introduce more layers, which will also result in relatively thick films that may exhibit higher mechanical stress. In order to reduce weight, there may be parts with a relatively small aspect ratio in the system, and the film stress will deform these parts, thereby increasing the wavefront distortion of the entire system.
Military systems must withstand large fluctuations in temperature, temperature, and corrosion from salt spray, smoke, and other pollutants in the air. Some membranes will absorb water, coupled with temperature changes, the performance of the membrane may change. It can be seen that the performance stability and durability of the film are also factors that need to be considered.
The optical thin film deposition solution
There are many deposition techniques for coating optical thin films, and different coating processes have different effects on the stability, durability, laser damage threshold, and internal stress of the film. Optical engineers should have a basic understanding of these deposition techniques' characteristics, advantages, and limitations.
Thermal evaporation (using resistance heating or electron beam heating) is by far the most widely used method. Its advantage is that the method has a wide range of work (from ultraviolet to far-infrared) and low cost. The biggest disadvantage of this method is that it produces a porous film, which easily absorbs moisture, thereby changing the effective refractive index of the film, making it difficult to maintain the required film performance when exposed to changes in environmental temperature and humidity.
In addition, the porous membrane layer is prone to contain defects that lead to the deterioration of the surface quality, and the thermal evaporation membrane layer has the worst mechanical durability among all deposition techniques.
Ion-assisted deposition (IAD) is an upgrade of thermal evaporative deposition. It uses charged ions to compress each layer of deposition. IAD provides a denser optical thin film. IAD deposition technology achieves the best balance between durability and performance, especially in the mid-wave infrared range of 3μm to 5μm.
In ion sputter deposition (IBS), a beam of high-energy ions is directed at a target (usually composed of metal or oxide), and atoms or molecules of the target are sputtered with high energy. These particles then flow out of the source and are then deposited on the substrate. IBS produces a completely dense optical thin film, which avoids the water absorption of the film, and is also very stable when the environment changes.
The materials deposited by IBS have reproducible refractive index characteristics, coupled with precise control of the thickness of the film, the film has very high precision, and it can consistently perfectly match the actual film with the design expectations. This is in the production of multi-spectral films. And the film layer that satisfies a wide range of angles and specific polarization characteristics is of great significance.
Compared with evaporative deposition, IBS uses a limited range of materials, which is not a problem in the visible and near-infrared bands. Since ZnS and fluoride materials are not compatible with IBS, it becomes a problem in the range of 3 μm to 5 μm. A potential problem with all dense optical thin films is that they may contain stresses that negatively affect wavefront distortion.
As a leading infrared optical lens manufacturer, QUANHOM has developed some methods to control such potential problems. For example, the post-film annealing process is used to reduce the internal stress, pre-calculated and purposefully created a surface error, and then the stress caused by the film is corrected.
The infrared optical lenses produced by QUANHOM adopt a reasonable and good optical thin-film design, which can meet the system's performance indicators. If you still have some doubts about the optical thin film design after reviewing the above, you can contact us for a comprehensive solution.
As a professional manufacturer of Opto-electromechanical components, we have always been committed to producing a variety of high-quality infrared thermal imaging lenses (including LWIR, MWIR, and SWIR). We have a professional production team, a strict quality inspection system, and control quality from product design to export. At the same time, we will also provide thoughtful one-stop service and effective solution technology according to the actual needs of customers. If you are interested in our infrared optical lens, please contact us immediately!